Qu’est-ce qu’une Imprimante 3D 5 Axes ? Fonctionnement, avantages, applications…
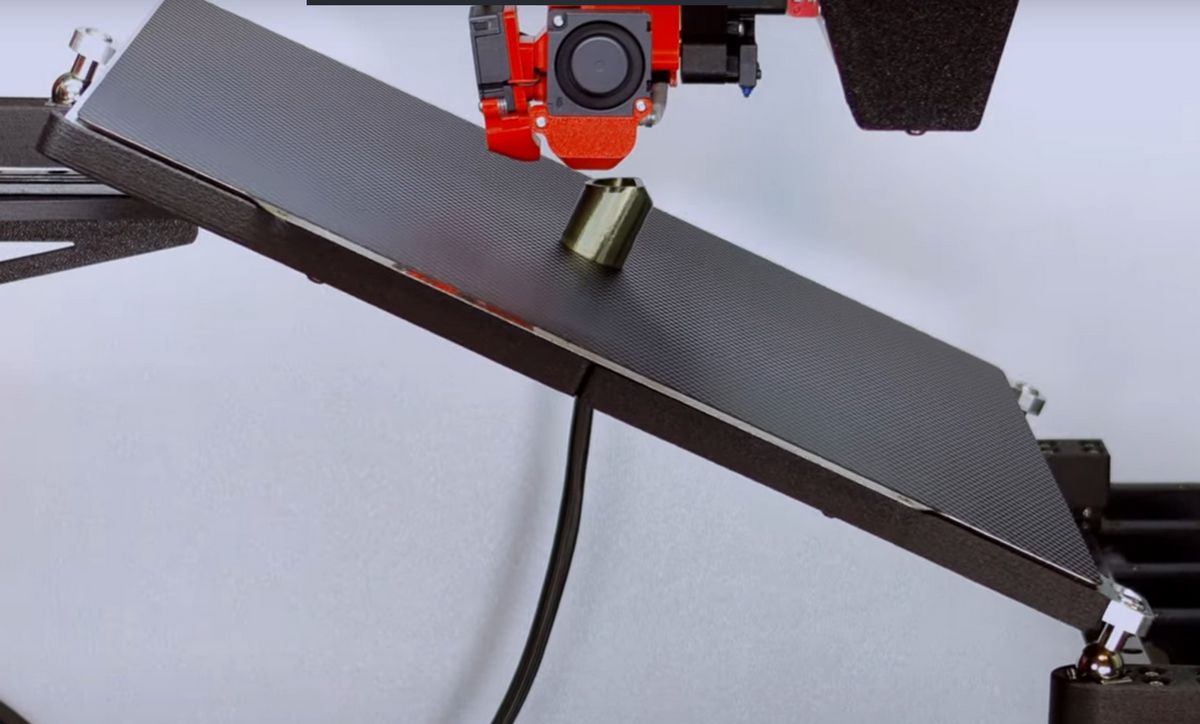
L’impression 3D traditionnelle, avec ses trois axes (X, Y, Z), a révolutionné la manière dont nous concevons et produisons des objets. Cependant, cette méthode de fabrication « couche par couche » présente des limitations inhérentes, notamment la nécessité de supports pour les surplombs et l’anisotropie des pièces (résistance inégale selon les axes). C’est là qu’intervient l’imprimante 3D 5 axes, une technologie avant-gardiste qui promet de libérer la fabrication additive de ses contraintes les plus fondamentales, ouvrant la voie à des géométries plus complexes, des pièces plus robustes et des processus plus efficaces.
Qu’est-ce qu’une Imprimante 3D 5 Axes ?
Le fonctionnement d’une imprimante 5 axes est fondamentalement plus complexe que celui d’une 3 axes, principalement au niveau logiciel :
- Modélisation 3D : Le processus commence toujours avec un modèle 3D conçu dans un logiciel de CAO.
- Logiciel de Tranchage (Slicer) Avancé : C’est le cœur de l’innovation 5 axes. Un slicer traditionnel ne peut pas gérer les mouvements rotatifs. Les imprimantes 5 axes nécessitent des logiciels CAM (Computer-Aided Manufacturing) ou des slicers spécialisés capables de :
- Analyser la géométrie de la pièce pour identifier les zones critiques (surplombs, angles faibles).
- Déterminer l’orientation optimale de la buse et/ou de la pièce pour chaque segment d’impression.
- Générer un chemin d’outil (toolpath) complexe qui utilise les 5 axes pour déposer le matériau de manière non planaire, c’est-à-dire en suivant les courbes de l’objet plutôt qu’en empilant des couches parfaitement horizontales.
- Déroulement de l’Impression : L’imprimante exécute les commandes du G-code généré par le slicer/CAM, inclinant et tournant la buse ou le plateau selon les besoins pour construire la pièce de manière optimisée.
Comment fonctionne l’Impression 3D 5 Axes ?
Le format 3MF a été développé par le Consortium 3MF (incluant des géants comme Microsoft, HP, Autodesk, Dassault Systèmes, etc.) pour pallier les lacunes du STL et offrir une solution plus complète et fiable pour la fabrication additive moderne.
Comment ça marche ?
- Le 3MF est un format basé sur XML, qui regroupe toutes les informations pertinentes dans un seul fichier compressé (.3mf). C’est comme un fichier ZIP contenant toutes les données nécessaires.
- Il décrit la géométrie de l’objet, mais aussi bien plus.
Avantages (par rapport au STL) :
- Richesse d’Informations Intégrées :
- Couleur et Texture : Le 3MF peut inclure des informations sur la couleur (par sommet, par face) et les textures (standard, PBR – Physically Based Rendering), permettant des impressions photo-réalistes.
- Matériaux Multiples : Il peut définir et attribuer différents matériaux à différentes parties du modèle dans un seul fichier, essentiel pour les imprimantes multi-matériaux.
- Unités de Mesure : Les unités sont explicitement définies dans le fichier, éliminant les problèmes d’échelle.
- Informations sur les Supports : Peut inclure des données sur les supports générés ou d’autres instructions spécifiques à l’impression.
- Métadonnées : Permet d’intégrer des informations sur l’auteur, la licence, les propriétés du modèle, etc.
- Géométrie Fiable et Améliorée :
- Conçu pour assurer un maillage « étanche » et sans erreur (« watertight »), réduisant considérablement les problèmes courants avec les STL (trous, normales inversées).
- Peut représenter des informations volumétriques (pas seulement la surface) et même des géométries complexes (comme des formes implicites) plus efficacement.
- Un Fichier, Tout Compris : Au lieu d’avoir un fichier STL pour la géométrie, des fichiers images pour les textures, et des notes pour les matériaux, le 3MF contient toutes ces données dans un seul paquet. Cela simplifie la gestion des projets, le partage et réduit les erreurs.
- Ouvert et Extensible : Le format est ouvert et peut être étendu pour de futures fonctionnalités ou des besoins spécifiques de l’industrie (par exemple, des extensions pour la découpe de tranches, la gestion des matériaux de construction, etc.).
Avantages révolutionnaires de l’Impression 3D 5 Axes
L’ajout de ces deux axes supplémentaires débloque des capacités qui étaient auparavant des limitations majeures pour l’impression 3D :
- Réduction Drastique, voire Suppression des Supports : C’est l’avantage le plus significatif. En inclinant la pièce, les surplombs peuvent être imprimés sous un angle optimal, ne nécessitant ainsi plus (ou très peu) de structures de support. Cela réduit le gaspillage de matière, le temps de post-traitement et améliore l’esthétique des surfaces.
- Amélioration des Propriétés Mécaniques (Isotropie) : Les pièces imprimées en 3 axes sont généralement anisotropes, c’est-à-dire plus faibles entre les couches. En imprimant le long de contours courbes ou en croisant les chemins d’extrusion avec les couches adjacentes grâce aux mouvements 5 axes, l’adhérence inter-couches est améliorée. Les pièces finales sont alors plus résistantes dans toutes les directions, se rapprochant des propriétés des pièces moulées ou usinées.
- Meilleure Qualité de Surface : En imprimant directement sur des surfaces courbes, l’effet de « marche d’escalier » (stair-stepping) caractéristique des couches est considérablement réduit, ce qui donne des pièces avec une finition de surface plus lisse et plus esthétique.
- Impression Directe sur des Composants Existant : La capacité d’orienter la buse permet d’imprimer directement sur des pièces ou des surfaces déjà existantes, ouvrant la voie à la réparation de pièces endommagées ou à l’ajout de fonctionnalités sur des objets préfabriqués.
- Liberté de Conception Accrue : Les designers ne sont plus contraints par les limites des surplombs ou de l’orientation des couches, permettant la création de géométries encore plus complexes et optimisées.
Défis et obstacles à l’adoption
Malgré ses avantages indéniables, l’impression 3D 5 axes fait face à plusieurs défis :
- Complexité Logicielle : Le développement de slicers/CAM performants capables de gérer efficacement les 5 axes est le principal obstacle. Le logiciel doit être capable de générer des trajectoires sans collision et d’optimiser les angles d’impression.
- Coût Élevé : Les imprimantes 5 axes sont des machines complexes, ce qui les rend beaucoup plus chères que leurs homologues 3 axes.
- Complexité d’Opération et de Calibration : La mise en œuvre et le maintien d’une imprimante 5 axes sont plus exigeants, nécessitant des compétences techniques avancées.
- Volume d’Impression Réduit : Le mouvement du plateau ou de la tête peut parfois réduire le volume d’impression utile pour certains designs.
Applications potentielles et actuelles
L’impression 3D 5 axes est actuellement un domaine de recherche et développement actif, mais elle commence à trouver des applications prometteuses dans des secteurs exigeants :
- Aéronautique et Spatiale : Pour des pièces légères et ultra-optimisées qui requièrent une intégrité structurelle maximale et une absence de défauts.
- Médical : Fabrication d’implants, de prothèses ou d’orthèses avec des formes complexes et une résistance isotrope cruciale pour la performance et la sécurité.
- Fabrication d’Outils et de Moules : Création de moules et d’outils avec des détails et des finitions de surface supérieures, sans la nécessité de post-traitement intensif.
- R&D et Prototypes Avancés : Pour repousser les limites de la conception de produits et tester de nouvelles approches de fabrication.
- Réparation et Personnalisation : Ajouter de la matière ou réparer des pièces existantes avec précision et robustesse.
L’imprimante 3D 5 axes représente une avancée majeure qui transcende les limites fondamentales de l’impression 3D traditionnelle. En permettant de fabriquer des pièces sans supports, avec une résistance améliorée et une meilleure finition de surface, elle ouvre la porte à des applications industrielles de haute valeur. Bien que la technologie soit encore coûteuse et que les logiciels soient en constante évolution, le potentiel de la fabrication additive 5 axes est immense. Elle nous rapproche d’une véritable « liberté de fabrication tridimensionnelle », où les contraintes géométriques s’estompent au profit de l’innovation et de l’efficacité.