Les Différents Remplissages en Impression 3D : L’Art d’allier Solidité et Efficacité
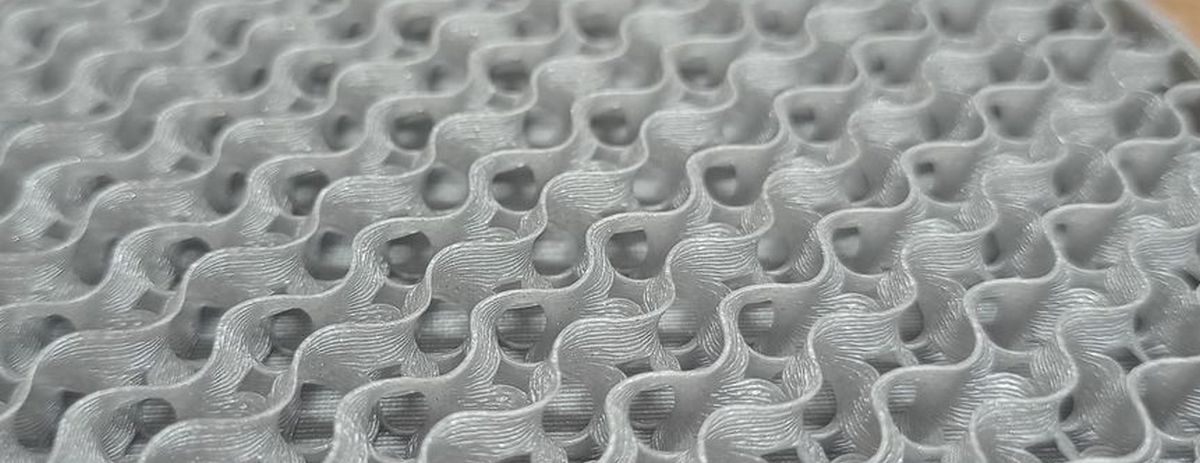
En impression 3D FDM (Fused Deposition Modeling), la pièce n’est que très rarement imprimée entièrement pleine. Une structure interne, appelée remplissage ou « infill », est créée à l’intérieur de l’objet. Ce remplissage est un paramètre crucial qui détermine non seulement la solidité et la résistance de la pièce, mais aussi son poids, le temps d’impression et la quantité de matière consommée.
Le choix du bon type de remplissage et de sa densité est un équilibre subtil qui doit correspondre aux exigences fonctionnelles de votre pièce. Plongeons dans les différents motifs de remplissage et leur impact sur la solidité.
Qu’est-ce que le Remplissage et Pourquoi est-il essentiel ?
Le remplissage est le motif interne de l’objet imprimé en 3D. Le logiciel de tranchage (slicer) génère cette structure en fonction de vos paramètres. Il est essentiel pour plusieurs raisons :
- Support Structurel : Il soutient les couches supérieures de la pièce et empêche les déformations ou l’effondrement des parois.
- Solidité et Rigidité : Une pièce avec un remplissage adéquat sera plus résistante aux contraintes mécaniques (compression, traction, flexion, torsion).
- Poids de la Pièce : Un remplissage moins dense réduit considérablement le poids final de l’objet.
- Consommation de Matériau : Un remplissage élevé utilise plus de filament.
- Temps d’Impression : Plus le remplissage est dense ou complexe, plus l’impression sera longue.
Facteurs Clés influençant la Solidité au-delà du Remplissage
Avant de détailler les motifs, il est important de noter que d’autres paramètres jouent un rôle majeur dans la solidité globale de la pièce :
- Nombre de Périmètres (ou épaisseur des parois) : Les parois extérieures (shells ou perimeters) sont souvent le facteur le plus important pour la résistance à la flexion et à la rupture. Une augmentation du nombre de périmètres aura souvent un impact plus significatif sur la solidité qu’une augmentation équivalente du remplissage.
- Matériau : Le type de filament (PLA, PETG, ABS, Nylon, PC, Composites) est le déterminant principal de la résistance.
- Hauteur de Couche : Des couches plus fines peuvent améliorer la cohésion entre les couches.
- Orientation de l’Impression : La direction des couches par rapport aux contraintes appliquées est cruciale. Les pièces sont généralement plus solides le long des couches que perpendiculairement à elles.
Les Motifs de Remplissage les plus courants et leur Solidité
Voici un aperçu des motifs de remplissage les plus fréquemment utilisés dans les trancheurs et leurs caractéristiques en termes de résistance :
Lignes (Line / Rectilinear)
-
- Description : Simple motif de lignes parallèles qui alternent d’une couche à l’autre (souvent à 90°).
- Solidité : Bonne dans les directions des lignes, mais plus faible dans les directions perpendiculaires. Non-isotrope. Rapide à imprimer.
- Usage : Prototypage rapide, pièces non soumises à de fortes contraintes.
Grille (Grid)
-
- Description : Des lignes parallèles qui se croisent à 90° sur la même couche, formant un motif de grille.
- Solidité : Meilleure que les simples lignes, mais peut créer des « poches d’air » sous les couches supérieures (effet de coussin).
- Usage : Usage général, pièces de support simples.
Triangles (Triangles)
-
- Description : Motif de lignes qui s’intersectent pour former des triangles réguliers.
- Solidité : Bon équilibre entre solidité et consommation de matière. Les triangles sont des formes structurelles très stables. Offre une résistance plus équilibrée.
- Usage : Pièces nécessitant une bonne solidité sans être critiques.
Hexagone / Alvéolaire (Honeycomb / Hexagon)
-
- Description : Crée des cellules hexagonales, imitant la structure d’une ruche.
- Solidité : Excellent rapport solidité/poids. Très bonne répartition des forces grâce à la structure cellulaire qui résiste bien à la compression et à la torsion. Considééré comme l’un des meilleurs pour la solidité générale.
- Usage : Pièces fonctionnelles, composants structurels, supports pour des charges modérées à élevées.
Gyröide (Gyroid)
-
- Description : Une structure 3D complexe, non-linéaire et entrelacée, ressemblant à une éponge mathématique.
- Solidité : Très haute résistance isotrope (uniforme dans toutes les directions). Excellente distribution des contraintes. Permet un bon drainage de l’excès de résine dans les impressions SLA/DLP.
- Usage : Pièces soumises à des contraintes multidirectionnelles, composants aéronautiques légers, pièces esthétiques avec des surfaces transparentes.
Cubes / Subdivision Cubes (Cubic / Cubic Subdivision)
-
- Description : Motif 3D composé de cubes (ou subdivisions de cubes) empilés.
- Solidité : Offre une très bonne solidité générale, particulièrement résistant aux forces de compression et aux impacts. Également isotrope dans ses versions 3D.
- Usage : Pièces nécessitant une grande résistance aux chocs et aux écrasements.
Concentrique (Concentric)
-
- Description : Le remplissage suit les contours extérieurs de la pièce, réduisant la taille à chaque ligne vers l’intérieur.
- Solidité : Très bon pour la compression perpendiculaire aux couches. Idéal pour les pièces flexibles (TPU) car il respecte la flexibilité du matériau. Moins solide pour les forces latérales.
- Usage : Pièces flexibles, bouchons, joints, coques, où la flexibilité ou la compression est primordiale.
Cross 3D
-
- Description : Certains slicers peuvent proposer des motifs plus avancés qui incorporent des éléments de « croix » dans les trois dimensions, ou qui sont des variations du motif de grille conçu pour offrir une meilleure répartition des forces. Cela pourrait ressembler à des structures en « X » ou en croix se répétant et se superposant de manière à créer une interconnexion plus robuste à travers les couches.
- Solidité : Vise à offrir une solidité plus isotrope (uniforme dans toutes les directions) en distribuant les charges de manière plus efficace dans l’espace 3D. Ces motifs sont généralement plus résistants que les grilles 2D.
- Usage : Pièces fonctionnelles nécessitant une bonne résistance dans toutes les directions, mais potentiellement moins optimisées en matière de poids que des motifs comme le Gyröide ou l’Hexagone 3D.
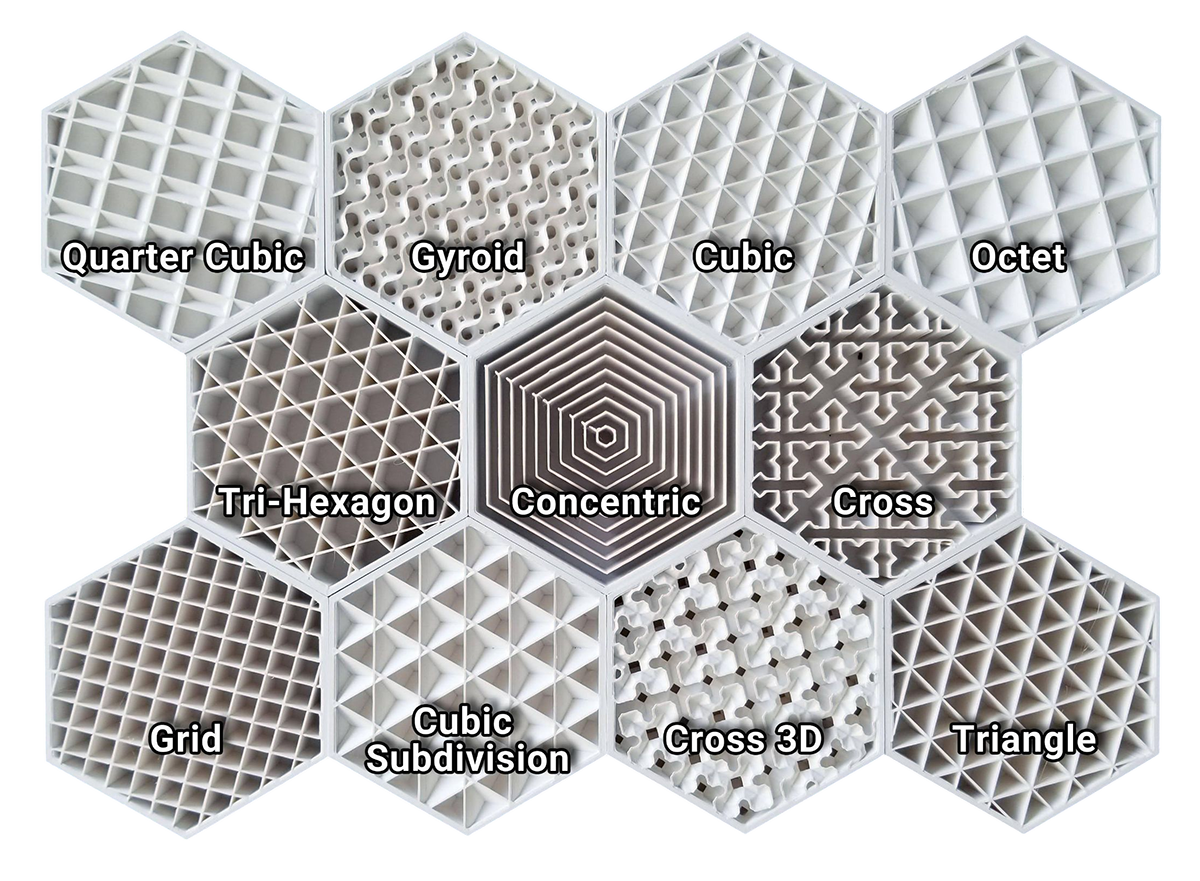
Densité de Remplissage : Le pourcentage qui change tout
La densité de remplissage (exprimée en pourcentage, de 0% à 100%) est le paramètre le plus intuitif :
- 0% (Creux) : Pour les objets purement esthétiques, ou des boîtiers légers. Très rapide et économique.
- 10-20% : Souvent suffisant pour la plupart des pièces fonctionnelles courantes qui ne sont pas soumises à de fortes contraintes. Bon équilibre.
- 20-40% : Pour les pièces qui doivent supporter des charges modérées ou qui nécessitent une certaine rigidité.
- > 40% : Réservé aux pièces soumises à des contraintes importantes. Au-delà de 60-70%, les gains de solidité sont marginaux par rapport à l’augmentation du temps et du coût. À ce stade, il est souvent plus efficace d’augmenter les périmètres ou de changer de matériau.
- 100% (Plein) : Pour des pièces critiques nécessitant une résistance maximale, ou si vous travaillez avec des matériaux flexibles qui ont besoin de masse pour fonctionner comme des joints d’étanchéité. Augmente considérablement le temps et le coût.
Le bon choix pour la bonne application
Choisir le bon remplissage est une décision éclairée. Pour une pièce nécessitant une solidité optimale, privilégiez un motif comme l’Hexagone ou le Gyröide avec une densité comprise entre 20% et 40%, et assurez-vous d’avoir un nombre suffisant de périmètres (au moins 3-4). Pour de simples prototypes, 10-15% en lignes ou grille suffira.
L’expérimentation est la clé ! N’hésitez pas à imprimer des échantillons avec différents réglages pour comprendre comment chaque motif et densité affecte les performances de vos pièces. C’est en maîtrisant ces paramètres que vous transformerez vos échecs en succès et que vos impressions 3D atteindront un niveau de solidité optimal.